Maintenance prédictive : définition et intérêt dans l'industrie
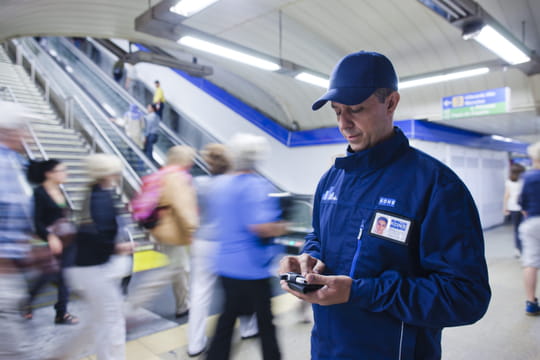
En quelques années, la maintenance prédictive a envahi et révolutionné le secteur de l'IoT. Définition, outils, applications… Découvrez l'essentiel de ce qu'il faut savoir sur cette technique de détection des pannes.
Qu’est-ce que la maintenance prédictive ?
La maintenance prédictive consiste à anticiper les défaillances à venir sur un équipement, un objet, un système, etc. Concrètement, il s’agit d’aller au-devant d’une panne ou d’un dysfonctionnement grâce au cumul d'un ensemble de données. En plein essor ces dernières années, la maintenance prédictive présente plusieurs avantages. Elle évite, par exemple, l’immobilisation d’un système de production en panne (avec les répercussions financières qui en découlent). Selon une étude publiée le 1er juillet 2021 par Senseye, fournisseur de solutions pour une gestion de l'état des équipements fondée sur l'IA, les multinationales du secteur industriel et manufacturier déplorent en moyenne 27 heures de temps d'arrêt machine par mois, pour un coût horaire moyen de 450 000 euros. La maintenance prédictive permet surtout d’anticiper ces pannes et offre la possibilité d’intervenir en évitant une réparation beaucoup plus coûteuse. Avec le prédictif, les coûts de maintenance sont réduits de 10 à 40% et le nombre de pannes divisé de moitié, rapporte de son côté le cabinet McKinsey.
Maintenance prédictive et intelligence artificielle
Ce sont les outils analytiques qui permettent de détecter les anomalies annonciatrices de pannes dans les données relevées par les capteurs. L'intelligence artificielle est ainsi essentielle au bon fonctionnement de la maintenance prédictive. Elle est à l'origine de la réduction de coûts. "Les services chargés de la maintenance sont parfois à l'origine de 60% des dépenses opérationnelles. Notre ambition est de réduire ces dépenses en utilisant l'intelligence artificielle pour analyser les données", explique Lukas Baur, vice-président de TeamViewer, éditeur du logiciel de contrôle à distance du même nom.
Maintenance prédictive et machine-learning
Le machine learning est une branche de l'intelligence artificielle qui permet, grâce à des algorithmes d'apprentissage automatique, d'analyser des données et de diagnostiquer des pannes à un stade précoce. Il s'agit de la technologie d'IA utilisée dans la maintenance prédictive (lire notre article : Pour assurer la maintenance prédictive, l'IoT passe à l'IA). L'éditeur français spécialisé dans l'IA at the edge Cartesiam a développé NanoEdge AI Studio V2, une plateforme qui simplifie la création de bibliothèques machine learning afin d'aider ses clients à qualifier des événements sur leurs machines de manière à pouvoir intervenir encore plus précisément.
Quels sont les différents types de maintenance ?
Avant que la maintenance prédictive ne devienne un élément clé de l'industrie 4.0, d'autres types de maintenance ont prévalu. La première est la maintenance curative, aussi appelée maintenance corrective ou réactive, qui consistait à intervenir sur une machine une fois qu'une panne survenait. Ensuite a été adoptée la maintenance préventive, dont l'objectif était de changer les pièces avant qu'une panne ne puisse intervenir. Avec la maintenance prédictive, la panne est anticipée dès que des signes avant-coureurs se font ressentir sur la machine, ce qui permet de changer les pièces au bon moment et de réduire les coûts en changeant des pièces inutilement.
Quelle différence entre la maintenance prédictive et préventive ?
La maintenance préventive se base sur l'estimation du cycle de vie d'un équipement. Des actions y sont effectuées régulièrement pour assurer son entretien dans la durée. Ce type de maintenance s'appuie sur la maxime "mieux vaut prévenir que guérir". La maintenance prédictive permet, grâce à des capteurs IoT, d'analyser la machine pour suivre en temps réel son état et de procéder à des réparations en temps voulu.
Quel est l'intérêt de la maintenance prédictive ?
La maintenance prédictive est source de ROI pour les entreprises. Selon l'entreprise Praxedo, qui développe des logiciels de gestion d'interventions pour les techniciens, les économies générées découlent de plusieurs conséquences :
- De la diminution des pannes et donc des temps d'immobilisation des équipements
- De l'allongement de leur durée de vie
- De l'amélioration de la fiabilité des équipements et donc une optimisation de la production
- D'une meilleure gestion des stocks de pièces de rechange
- D'une réduction des frais de maintenance.
D'après une étude publiée en 2017 par le cabinet Vanson-Bourne, chaque heure d'arrêt non planifiée coûte en moyenne 250 000 dollars, d'où l'importance pour les industriels d'éviter les pannes.
Quels sont les paramètres de détection ?
Les vibrations constituent l’un des principaux paramètres de détection d’une défaillance ou d’un dysfonctionnement. Dans le secteur industriel, la plupart des entreprises disposent de machines conçues pour pouvoir fonctionner sans vibration. De ce fait, la surveillance vibratoire permet d’identifier très rapidement un dysfonctionnement sur une machine, des vibrations anormales ressenties sur la machine annonçant une panne à venir.
D'autres paramètres peuvent également être suivis, comme la température, la pression des machines ou le son. En optant pour une maintenance prédictive, l’entreprise a la possibilité de détecter le défaut de sa machine avant sa manifestation et d’intervenir avant que la panne ne se produise.
La maintenance prédictive dans l'automobile
Selon les résultats de l'enquête menée en 2021 par Senseye, l'automobile est le secteur le plus touché par les temps d'arrêts-machines. Les sites perdent en moyenne 29 heures de production par mois au coût horaire estimé à 1,1 million d'euros. Pour 67% des entreprises de ce secteur interrogées, la maintenance prédictive est devenue un objectif stratégique. D'autant plus avec l'essor des véhicules connectés, qui permettent de collecter de nombreuses informations. Par exemple, avec son offre Michelin Tire Care, le fabricant français assure la maintenance prédictive de ses pneumatiques sous forme de service à ses clients.
La maintenance prédictive dans l'industrie
La maintenance prédictive domine particulièrement le marché de l'industrie car elle s'applique notamment aux machines tournantes. La crise sanitaire du coronavirus a par ailleurs accéléré le déploiement de la maintenance prédictive dans l'industrie, afin d'éviter aux techniciens de se déplacer inutilement (lire notre article : La crise accélère le déploiement de solutions de maintenance à distance). L'étude de Senseye montre que plus des deux tiers (72%) des grandes entreprises industrielles interrogées considèrent la maintenance prédictive comme un objectif stratégique. Une entreprise sur cinq (20%) a d'ailleurs constitué une équipe en interne pour déployer des projets de maintenance prédictive.
La maintenance prédictive pour les ascenseurs
Vous faites partie de celles et ceux qui ont la hantise de se retrouver bloqué dans un ascenseur ? Avec la maintenance prédictive et l’IoT, il devient possible de réparer une panne d’ascenseur avant que celle-ci ne se produise. Les principaux acteurs du marché de l’ascenseur se sont ainsi lancés dans une course aux services de maintenance prédictive pour leurs équipements, avec des ascenseurs toujours plus connectés et reliés à l’intelligence artificielle. A la clé, une résolution des problèmes avant qu’ils ne surviennent, et une sécurité optimale pour les usagers. La start-up parisienne WeMaintain a observé une division par trois des pannes au bout de 6 mois de maintenance prédictive. Plus de 10% du parc géré par l'ascensoriste finlandais Kone était connecté en juin 2020. Le groupe prévoit de connecter l'ensemble de ses nouveaux appareils pour proposer des services IoT d'ici 2022.
Les outils de la maintenance prédictive
Il existe aujourd'hui une multitude d'outils au service de la maintenance prédictive. En premier lieu : les capteurs IoT à installer sur les équipements concernés. Parmi ceux-ci, les capteurs BoB mis au point par Cartesiam et Eolane ou les Brainium Edge AI d'Octonion, qui mêlent IA et IoT pour surveiller des machines en continu. Le deuxième outil phare est la plateforme IoT, pour collecter et stocker les données. Des algorithmes de machine-learning sont par ailleurs mis au point pour assurer la maintenance prédictive des équipements. Quatrième outil : l'application, pour prévenir le technicien en temps réel.